To overcome various machining challenges and boost productivity, Seco has introduced new toolholders, PCBN inserts, round carbide inserts and extra-long solid carbide drills with enhanced versatility and tool life. These innovative products are aimed at applications ranging from general ISO turning to high-volume hard turning and deep hole drilling.
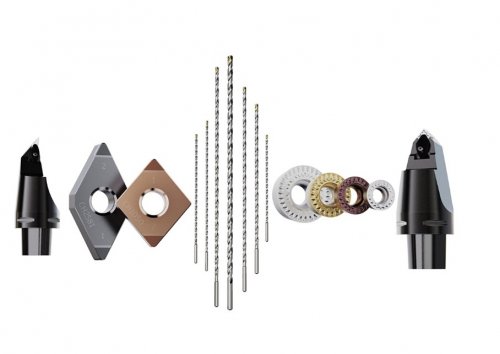
Cost-saving X-tra Long Solid Carbide Drills – 40xD-60xD
Manufacturers that drill holes at depths from 40xD to 60xD want to lengthen tool life and reduce tooling costs. New Seco X-tra Long Solid Carbide Drills provide more than 15% greater tool life than other extra-long solid carbide drills.
Seco X-tra Long Solid Carbide Drills achieve fast, reliable performance in steel, stainless steel and cast iron, as well as good performance in Inconel®, titanium and hardened steel, all on standard machining centers.
Unique tool geometry and coating eliminate chipping and sudden breakage while they minimize flank and center wear. A ground edge prep produces smoother cutting edges, greater evenness and closer tolerances than brushing. Seco X-tra Long Solid Carbide Drills maintain specified drilling depth after up to three reconditioning cycles.
CH1050 and CH2581 PCBN inserts for process stability
Two new Seco grades of PCBN inserts offer ideal performance in high-volume production of automotive and other industry components. The CH1050 grade is designed for finishing and the CH2581 for semi-interrupted cuts.
With a substrate grade and unique Seco nanolaminate PVD coating designed to achieve high surface quality requirements, CH1050 also offers high-accuracy edge prep through a new grinding process. Designed for extended tool life and lower cost per part, CH1050 promotes high output and reduced scrap or rework.
CH2581 achieves greater process stability and reduced tool breakage with a versatile, forgiving grade specifically designed for semi-interrupted cuts. Its high-accuracy edge prep and next-generation Seco PVD coating enable faster speeds and higher throughput for reduced part costs.
MF2 chipbreaker on RCMT/RCGT round, positive-style ISO-turning carbide inserts with chip control
Many round turning inserts suffer from poor chip control, but Seco MF2 chipbreaker on RCGT/RCMT inserts maintains favorable chip control at higher speeds and feeds, especially with dynamic turning. One series of stable, durable carbide round insert grades handles a wide range of turning operations from roughing to finish turning.
Seco’s unique chipbreaker geometry and strong insert shape provide versatile, reliable performance in tough operations, including heavy intermittence and rough skin. In a general engineering environment with materials ranging from smeary low-carbon steels to stainless steels, titanium and heat-resistant super alloys (HRSA), these versatile inserts outperform pointed tools.
On parts with wide, deep grooves, pockets or cavities – even in difficult-to-cut materials – MF2 chipbreaker on RCMT/RCGT inserts tackles complex parts with fast production.
Better surface finishes with Seco-Capto MTM JETI Toolholders for general ISO turning
Seco have utilized their unique 3D-printed coolant clamp to deliver Jetstream Tooling® high-pressure cutting fluid directly to the cutting edge. With a range of single-screw coolant clamp options for specific applications and depths of cut, these toolholders provide fast setup and indexing, making chip control less of a challenge on 45° B-axis multi-tasking machines.
Seco-Capto MTM JETI Toolholders allow for the use of shorter tooling with greater reach, less overhang and reduced collision risk. The decrease in vibration and chatter improve machining results, even with materials that require high-pressure cutting fluid. The toolholder design also enables shops to optimize production and use the same machining tools on more than one spindle.
Seco innovation for production efficiency
The recently launched tools, toolholders and chipbreakers move manufacturers toward better results easier, more quickly and with cost savings. “We're focused on developing new ways for our customers to solve age old problems while taking full advantage of their machine tools,” said Mia Bökmark, Vice President Product Offer & Innovation at Seco. “We draw on more than 80 years of toolmaking experience to offer solutions for the real challenges in every shop.”
For more information on the features and specifications of these new Seco products, please contact a local Seco representative or visit http://www.secotools.com/.
###
Seco new product solutions
With its origins in Fagersta, Sweden and present in more than 75 countries, Seco is a leading global provider of metal cutting solutions for indexable milling, solid milling, turning, holemaking, threading and tooling systems. For nearly 100 years, Seco has driven excellence throughout the entire manufacturing journey, ensuring high-precision machining and high-quality output.
For the latest innovations and cutting-edge products, visit www.secotools.com.