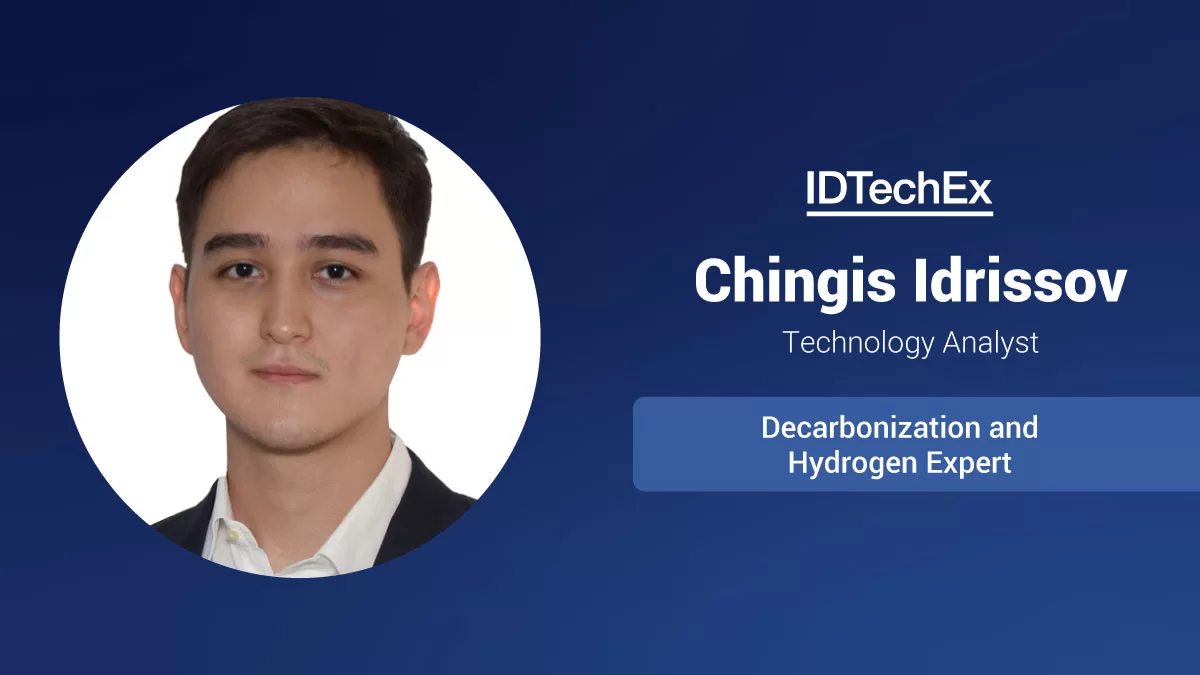
Author: Chingis Idrissov, Technology Analyst at IDTechEx Green hydrogen is increasingly recognized as a clean industrial feedstock and the future’s energy carrier. Central to green hydrogen production is the water electrolyzer. Historically, the alkaline water electrolyzer (AWE) has dominated the market due to its maturity and development. However, over the last two decades, the proton exchange membrane electrolyzer (PEMEL) has seen rapid advancement, swiftly moving into commercial applications. Particularly popular in Europe, PEMEL stands out for its high energy efficiency and compatibility with intermittent renewable energy sources. The PEM electrolyzer shares many materials and components with the PEM fuel cell (PEMFC), benefiting greatly from advancements in the fuel cell sector. Initiated by NASA, PEMFC technology has evolved significantly, leading to both PEMEL and PEMFC becoming relatively established technologies. Yet, they still face numerous challenges. The burgeoning green hydrogen market is driving demand for electrolyzer systems, in turn generating demand for electrolyzer materials and components. This surge presents a vast opportunity for material and component suppliers, along with various industry players, to leverage this growth, innovate, and introduce new products. This research article delves into the critical materials and components of the PEM electrolyzer, highlighting key issues and opportunities in this evolving sector. For more insights on this topic, please refer to the IDTechEx report, “Materials for Green Hydrogen Production 2024-2034: Technologies, Players, Forecasts“.
|
||
Simplified schematic of proton exchange membrane electrolyzer (PEMEL) cell components. Source: IDTechEx |
||
Proton exchange membrane (PEM) The proton exchange membrane (PEM) is the backbone of the electrolyzer, situated between the cathode and anode. PEMs facilitate the transfer of protons (H+ ions) from the anode to the cathode. They also provide electrical insulation between the electrodes and ensure that hydrogen and oxygen evolution reactions take place separately, thus achieving high-purity hydrogen output and avoiding mixing gases, particularly hydrogen in oxygen. The membranes are made of perfluorinated sulfonic-acid (PFSA) ionomers. Nafion, a brand of Chemours (originally developed by DuPont), is the incumbent and most well-known material used in PEMELs and PEMFCs. The market is dominated by established players like Chemours and W. L. Gore & Associates. However, these companies are still trying to innovate their products to achieve better performance. The main problem in improving PEMs is the trade-offs between performance, safety, and durability. This is because increasing performance requires thinner membranes for enhanced conductivity; however, that causes more hydrogen into oxygen gas crossover and faster membrane degradation. A common alleviation tactic explored in the industry is the use of a reinforcement layer, such as expanded polytetrafluoroethylene (PTFE), which the PFSA ionomer is then coated onto. Dealing with improvement trade-offs using new composite membrane materials will be key to advancing the technology. Despite the issues, PFSA membranes will continue as the incumbent material due to a lack of suitable market-ready alternatives. Hence, there is a significant market for membranes in the electrolyzer and fuel cell industries. Platinum group metal catalysts & the catalyst-coated membrane (CCM) Platinum (Pt) and iridium (Ir) catalyze the electrochemical hydrogen and oxygen evolution reactions occurring in the electrolyzer, respectively. The state-of-the-art materials used are platinum supported on carbon black (Pt/C) for the cathode and iridium black (Ir) or iridium oxide (IrOx) for the anode. The catalysts are combined with PFSA ionomer resins in the form of ink, which is then coated onto the membrane, producing the catalyst-coated membrane (CCM). CCM production is a key research avenue, as the performance of the electrolyzer largely depends on its properties. A key focus is the development of efficient and continuous roll-to-roll processes for CCM production, which can guarantee consistent performance, minimal loss of catalytic inks, and highly automated large-scale production. The more important research focus is the need to reduce iridium loading at the anodes. Current loadings of 1 – 2.5 g/kW of PEM electrolyzers are problematic, as future demand for PEM electrolyzers may put a significant strain on global iridium supply. To address this, catalyst manufacturers like Heraeus Precious Metals are introducing new products into the market that reduce iridium loading. These include iridium-ruthenium oxide (IrRuOx), which is already beginning to be used commercially. However, new supported iridium catalysts (similar concept to platinum supported on carbon) will eventually be needed to reduce dependence on iridium supply. Hence, significant opportunities exist to develop and introduce new catalyst products onto the market, which provide competitive performance to current Ir and IrOx while reducing the overall iridium loading to less than 1 g/kW. Gas diffusion layers (GDL) Gas diffusion layers (GDL), also known as porous transport layers (PTL), are another key component of the PEMEL cells. These components are present at both electrode sides and facilitate the transfer of water to the membrane, the removal of product gases (H2 & O2) from the electrodes, and the flow of electrons through the cell. Carbon paper is used as the cathode material, consisting of carbon fibers, PTFE and carbon black. The anode side relies on the use of titanium felt, which is coated with a thin layer of platinum metal. Titanium is needed for its corrosion resistance on the anode side, while platinum provides enhanced electrical conductivity and additional stability. These materials are here to stay and will form part of all PEMEL stacks. Carbon paper was developed thanks to the efforts of the PEM fuel cell industry and is already quite mature. Therefore, the main development focus is on the anode side to reduce the thickness of the titanium felt, optimize porosity, and reduce the amount of platinum that is needed. Platinum loading is especially important and can be reduced by employing advanced coating technologies, such as physical vapor deposition (PVD). Bipolar plates Bipolar plates serve as a physical barrier for separating cells. More importantly, these plates conduct electrons from the anode of one cell to the cathode of another, as well as provide channels for water and gas flow in the cells. Unlike in PEM fuel cells, where graphite bipolar plates can be used, PEM electrolyzers rely on titanium plates as they are more corrosion-resistant. Gold and platinum coatings are needed on the cathode and anode-facing sides, respectively, for extra corrosion resistance and low electrical contact resistance, similar to platinum used in titanium GDLs. Once again, these components benefit from highly developed metallic bipolar plate manufacturing from the PEM fuel cell industry. Examples of companies providing plate manufacturing technologies include Dana Inc, Schuler, Elcon Precision, and many more. All manufacturers use different technologies, each with their own pros and cons. Despite the high level of development, manufacturers can still optimize production by reducing material waste and speeding up production lines. Bipolar plate coating is an area that could benefit most from new concepts. For example, more advanced coating technologies, such as PVD, can reduce the use of precious metals. Alternatives to titanium could also be found to reduce the total manufacturing cost. This requires experimentation with various metal alloys and combinations of materials, such as titanium-coated stainless steel. The latter is seen as a promising option but still needs extensive testing in commercial operation. Gaskets & sealing materials Gaskets or seals are typically overlooked when designing electrolyzer stacks, but those components are equally vital. They serve as sealing elements, creating an interface between different components, such as the bipolar plates and the separator. These precision-engineered barriers ensure that gases, water, and cell components remain contained and separated as needed. Gaskets typically take the form of thin sheets or tapes, which are sandwiched between bipolar plates. Gasket materials are typically chosen to provide low hydrogen gas permeability to prevent leakage as well as chemical resistance to the acidic and oxidizing conditions in the electrolyzer. They also need to have adequate compressibility and mechanical properties to withstand compressive forces. Typical materials used include ethylene propylene diene monomer rubber (EPDM), fluorinated rubber (FKM), PTFE, and silicone. Preformed gaskets are the most common type. These are injection molded to fit the electrolyzer stack. Intricate designs of bipolar plates require thorough sealing, so gasket manufacturers typically partner with electrolyzer or bipolar plate suppliers. In this way, the manufacturer can deposit gaskets directly onto the customer’s components and ship them back to the customer. Gasket innovation strategies focus on optimizing the material and the manufacturing process, as well as bypassing the performing step by supplying resins that customers can deposit and cure themselves. Market outlook & strategic insights The electrolyzer component market is poised for significant expansion, with IDTechEx’s projections estimating its market value to reach an impressive US$31.7 billion by 2034. This growth is predominantly driven by the rapidly evolving green hydrogen industry. As seen in this article, there are vast opportunities for component supply and innovation in this market. IDTechEx’s “Materials for Green Hydrogen Production 2024-2034: Technologies, Players, Forecasts” report also provides similar insights into the materials and components used in alkaline water (AWE), anion exchange membrane (AEMEL) and solid oxide (SOEC) electrolyzers. Comprehensive lists of electrolyzer stack, component, and material suppliers are available, with case studies of key commercial innovations in the industry. Moreover, the report provides granular 10-year market forecasts, quantifying the demand for materials and components in tonnes, square meters (m2), and US$ million annually. Please refer to the report for deeper insight into the current trends and key opportunities in the water electrolyzer component market. To find out more about this report, including downloadable sample pages, please visit www.IDTechEx.com/GreenHydrogen. |