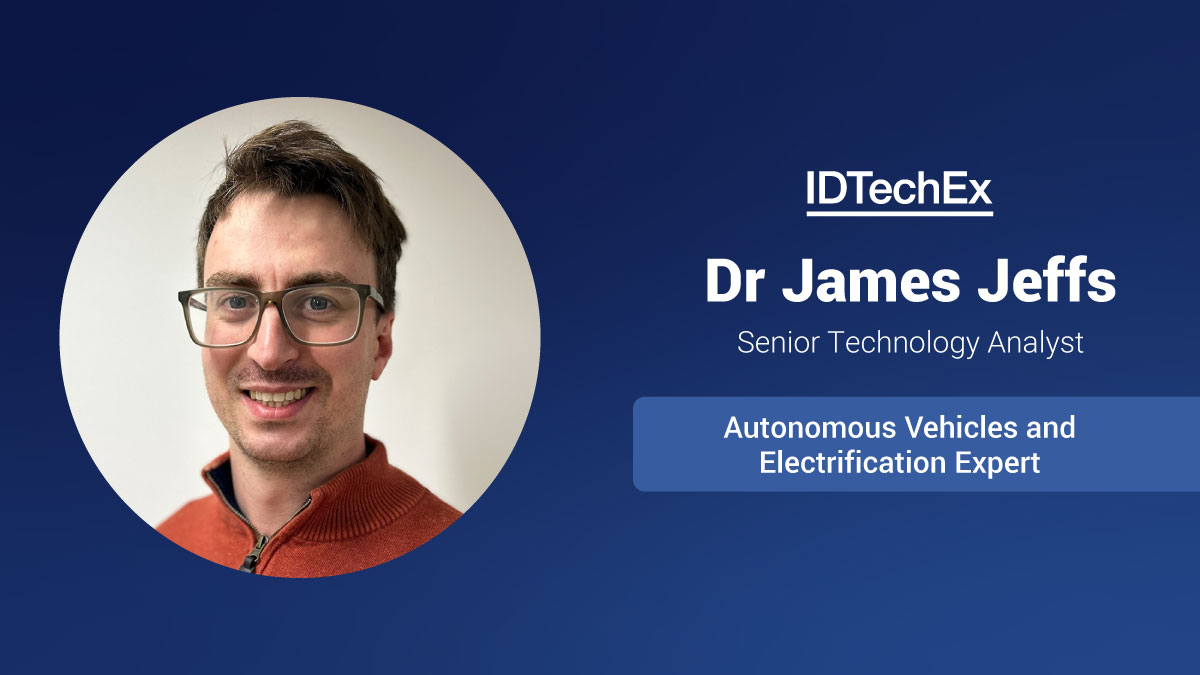
Author: Dr James Jeffs, Senior Technology Analyst at IDTechEx
One of the main reasons that electrification is so appealing in any industry is the reduction in operating costs offered by electric machines. This is especially true across the construction, agriculture, and mining (CAM) industries. Large machines with high uptimes, like mining haul trucks, can consume millions of dollars in fuel over their lifetime. As such, the potential total cost of ownership benefits are astronomical. Despite this, IDTechEx’s discussion with customers of CAM machines reveals that the upfront cost of electric alternatives is still too high. Customers would still rather stick to cheaper internal combustion machines, even though the lifetime cost of owning the machine would be higher.
The batteries used in electric CAM machines are the dominant reason that electric machines cost so much more than their internal combustion counterparts. This is a situation that has been improving. Prices have recently reduced from the US$500-1,000/kWh range to US$250-300/kWh. However, IDTechEx’s report “Battery Markets in Construction, Agriculture & Mining Machines 2024-2034” finds that even small machines, such as mini-excavators, can utilize batteries as large as 70kWh, equating to US$21,000. This is considerably more than the 40-50hp, small diesel engine that it would be replacing, not to mention the motor and power electronics that go along with it, although these are much cheaper than the battery.
There is light at the end of the tunnel, though. In early 2024, reports came out suggesting that CATL battery prices could be slashed. The automotive industry already benefits from a much higher volume than electric CAM machines, and pricing in the US$100-150/kWh range for lithium iron phosphate (LFP) batteries is the norm. But, the reports say that CATL’s VDA cells will be available for as little as US$57/kWh!
If the electric CAM machine makers had access to batteries at US$57/kWh, it would go a long way toward neutralizing the price premium that electric equivalents currently experience. Take the example above: the 70kWh battery would drop in price from US$21,000 to just under US$4,000.
For larger machines, the savings are even more stark. The biggest batteries that IDTechEx has seen in electric CAM machines belong to haul trucks. With operating weights in the hundreds of tonnes and uptimes of 20 hours per day, these machines require batteries as large as 1,600kWh. At current battery pricing, IDTechEx expects a battery that large to cost in the range of half a million dollars, very likely more. But, if CATL’s pricing were available, this would reduce to under US$100,000. These machines use so much fuel over their lifetimes that the battery premium is already repaid many times over. But cutting the upfront price of the machine by over US$400,000 would bring the pricing much closer to the internal combustion alternatives, and accelerate the time to seeing a return on the investment significantly.
It should be mentioned that LFP batteries tend to be cheaper than their common alternative nickel manganese cobalt (NMC) because they don’t offer the same performance. They tend to have lower gravimetric and volumetric energy densities, making them larger and heavier than NMC and, thus, harder to fit into a vehicle. In the automotive industry, this typically means that electric cars built with LFP batteries have shorter ranges than those with NMC batteries. For CAM machines being used in a commercial environment to get a job done, downtime is expensive. Customers will not accept electric machines if they don’t have enough battery capacity to complete a full day’s work. As such, a cheap LFP option is only feasible if its energy density is high enough to get the required capacity on whichever machine is being electrified. |
|
|
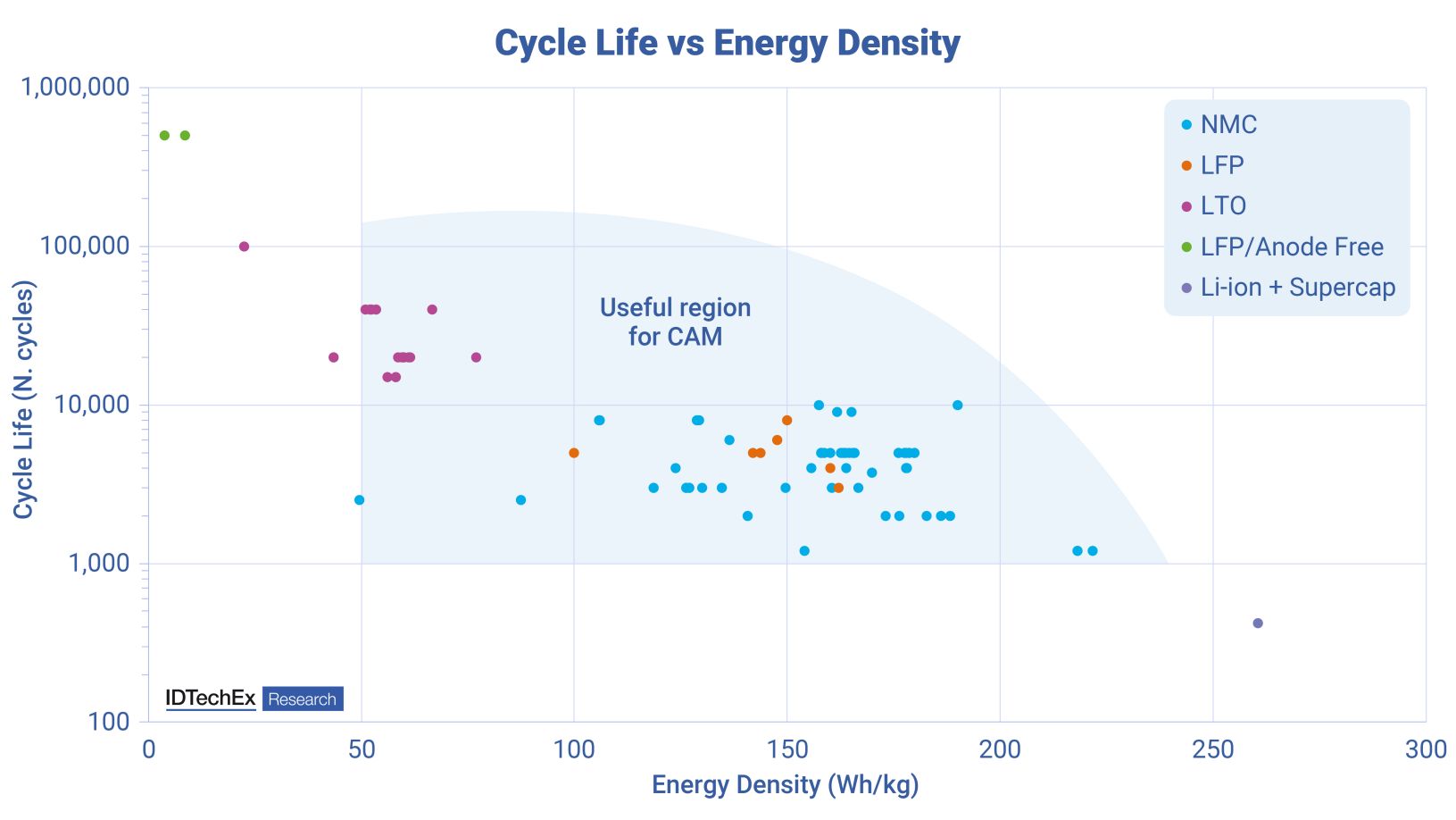
Typically, increased energy density comes with the trade-off of reduced battery lifetime. Source: IDTechEx |
||
IDTechEx’s report “Battery Markets in Construction, Agriculture & Mining Machines 2024-2034” analyses the battery requirements of 15 different machine types used across CAM markets. It finds that, out of the 15 machine types, nine are well suited to LFP battery technologies. For some machines, such as mini-excavators and tractors, a combination of highly energy-intensive work and smaller chassis space available for batteries means that NMC is preferable. But, for most machine types there is plenty of chassis space to overcome the volumetric energy density shortfall of LFP batteries, while battery weight is not too much of an issue for many CAM machines, meaning the gravimetric deficit of LFP batteries is irrelevant. This is confirmed by looking at the batteries currently used across electric CAM vehicles. IDTechEx’s database of more than 200 electric CAM vehicles shows that more than half of the options already available on the market use LFP batteries.
Other technologies with even greater cost reduction potential will come to challenge LFP’s dominance in the electric CAM machine industry. One hopeful is sodium-ion batteries, which use largely the same design as lithium-ion batteries but replace the expensive lithium charge carrier with cheaper sodium. However, lithium only makes up a very small amount of material in the battery and does not contribute significantly to the cost, meaning the cost reduction offered by sodium is only slight. Additionally, sodium-ion batteries typically have worse energy density than lithium ones, meaning there are fewer CAM machine applications where they could be used. Despite this, if sodium-ion can provide a cost-benefit, then there is definitely a place for it in the electric CAM machine market, especially in larger machines where the cost-benefit is more rewarding, and the machines can typically afford heavier and more voluminous batteries.
IDTechEx’s report “Battery Markets in Construction, Agriculture & Mining Machines 2024-2034” considers 10 different battery technologies at multiple stages of market readiness. Each technology is benchmarked against traits required for different CAM machine types offering a guide of which new technologies might fit where in this diverse industry.
US$57/kWh is a staggeringly cheap price for the automotive industry and one that will further drive down the cost of electric cars, encouraging widespread adoption and helping to reduce global carbon emissions. Unfortunately, with production volumes being so much lower for CAM machines, it is unlikely that electric CAM machines would benefit from these massive savings anytime soon. However, as volumes start to pick up, IDTechEx does expect prices to get closer to today’s typical automotive battery pricing. Maybe in the long term, electric CAM machine makers will be able to source batteries for as little as US$57/kWh. There is light at the end of the tunnel.
To find out more about this IDTechEx report, including downloadable sample pages, please visit www.IDTechEx.com/CAMBatteries.
For the full portfolio of batteries and energy storage market research from IDTechEx, please visit www.IDTechEx.com/Research/ES.
|